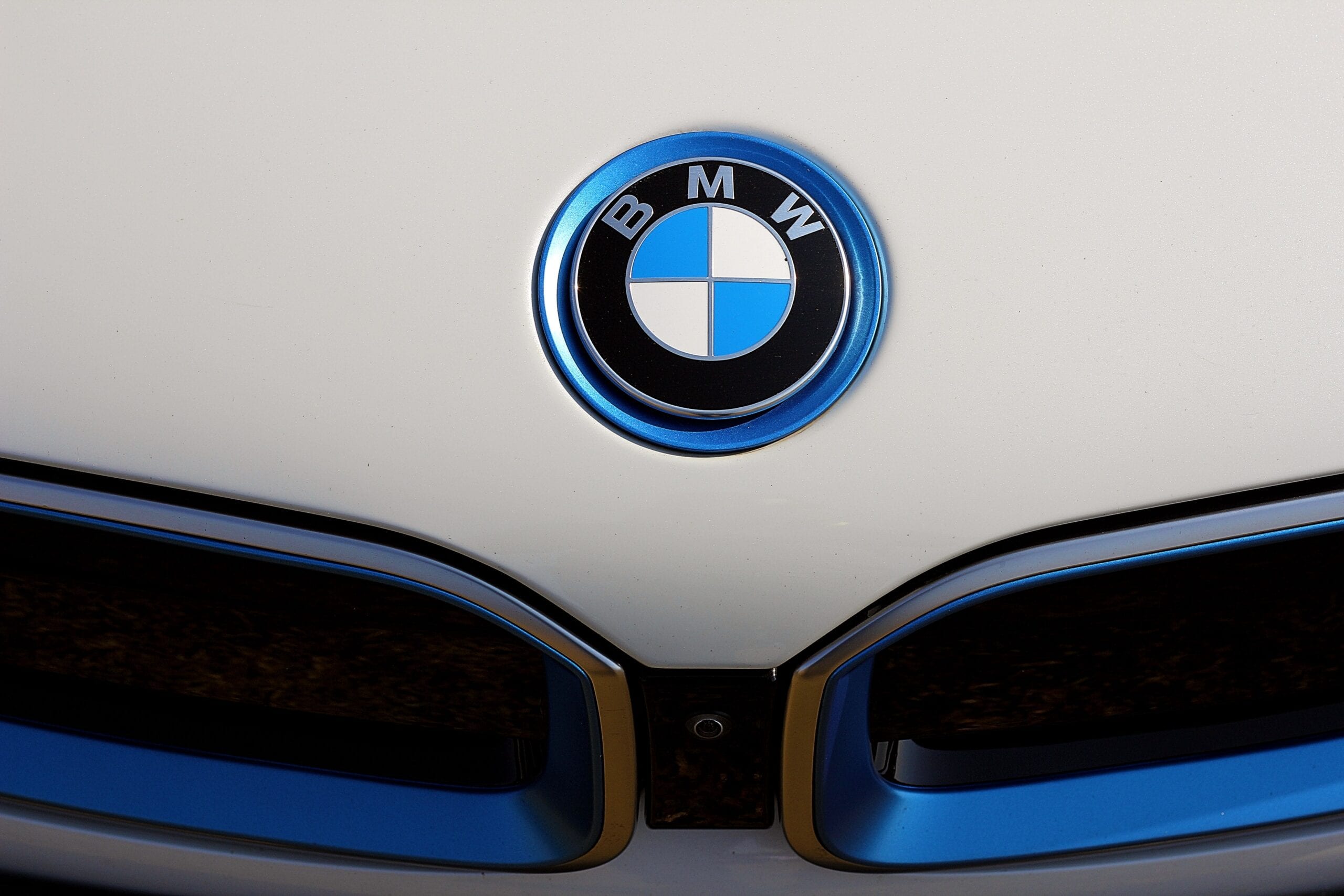
Gêmeos digitais, algoritmos, rastreabilidade e integração universal: A indústria 4.0 vista pela ótica da Siemens e da BMW.
30 de junho de 2019André Spínola e Lamisse Cavalcante
Fechando a série de artigos sobre as visitas realizadas na Alemanha, vamos mergulhar na indústria 4.0, a partir das percepções das megaindústrias globais Siemens e BMW.
Indústria 4.0
O conceito de indústria 4.0 é recente e faz alusão à quarta revolução industrial. Depois do vapor, nos anos 1700, da eletricidade nos anos 1800 e da computação nas últimas décadas dos anos 1900, a quarta revolução industrial se emoldura a partir da internet, que passa a conectar a tudo e a todos, em nuvem, alavancando algoritmos, capacidade de análise e processamento computacional e atuação em plataformas com trocas múltiplas de valor.
Como impactos diretos dessa nova revolução já podem ser vistos, além da maior produtividade e redução de custos, o controle do processo produtivo, a customização em escala, tomada de decisão em cima de big data, virtualização de operações, descentralização de tomada de decisões, rastreabilidade e modularidade de produção.
E isso tudo com uma amplitude e profundidade impressionantes e uma velocidade exponencial.
Nessa linha, falamos um pouco sobre o significado de “pensar digital” nesse artigo AQUI.
A Siemens e seus “gêmeos digitais”
A Siemens AG é uma holding industrial alemã com 15 divisões de negócios. São 372 mil funcionários, que geraram receitas globais de U$ 98 bi.
Desde a apresentação do CTO da empresa Bernard Quendt na Cebit, até o dia em que visitamos a planta de Amberg, a atuação por meio dos “gêmeos digitais” foi muito ressaltada e elencada como um dos grandes focos de ganho competitividade da empresa.

Não se trata de uma exclusividade da Siemens esse processo, mas é inegável sua eficiência na aplicação. São cópias digitais de produtos, processos ou equipamentos, que ajudam a aperfeiçoar processos fabris, prototipar alterações e novos produtos, diminuindo o tempo de lançamento no mercado.
O gêmeo digital é abastecido com dados operações reais e passa a simular condições de desempenho e funcionalidades desse seu “irmão”. Isso tudo antes de qualquer peça ser fabricada. Isso reduz o tempo de produção, desperdícios, amplia a flexibilidade e abrevia os prazos de lançamento. E, seguindo a mesma linha, ocorrem simulações de processos internos como, por exemplo, ergonomia dos trabalhadores e desenho de linhas de produção.
Na fábrica de Amberg, que funciona 24 horas por dia, de segunda a sexta, o carro chefe são os controladores lógicos programáveis Simatic (PLC), produzidos na casa de 12 milhões por ano. Atualmente, são fabricadas mais de 1.000 versões do PLC, solução que permite a automatização da produção e controle das máquinas e instalações. Seus ciclos de inovação são muito curtos, com até 5000 mudanças por produto e até 120 mudanças por dia. Como são 1200 produtos no portfólio, com alta flexibilidade e produção feita a partir dos pedidos, há até 350 mudanças na planta por dia.
Isso só pode acontecer por causa da digitalização, com 75% da cadeia de valor da fábrica sendo de responsabilidade de máquinas e algoritmos. Como a companhia trabalha com produtos de duração bastante estendida, a qualidade é inegociável e é medida em todos os passos da produção. Por se tratar de máquinas e equipamentos para fábricas, a vida útil passa dos 20 anos.
O cálculo de conformidade é totalmente on line e chega a incríveis 99,999%. Esses índices de defeitos caíram de 527 por milhão em 1991 para 9 em 2018. Isso explica-se pela prevalência de trabalho humano antes e o atual avanço tecnológico.
E vale ressaltar que, nos últimos 25 anos o faturamento da empresa aumentou 13 vezes, com o mesmo número de funcionários.
Há algo como 5 passos da cadeia de valor na Siemens, como base na adoção dos gêmeos virtuais:
- Design do produto – simulações térmicas, mecânicas, encaixes, dentre outros.
- Planejamento da produção – capacidades, layout planta e custos.
- Performance – parceiros constroem e ajustam.
- Execução da produção – todos os dados são acumulados para maior gestão de qualidade. Ensaio de campo.
- Serviços – é sobretudo manutenção e otimização das máquinas, com uma manutenção previsível.
Os ganhos de eficiência pela modularidade e rastreabilidade na BMW
Dispensando apresentações, a alemã BMW fabrica também veículos das marcas Rolls-Royce e Mini, em 30 fábricas em 14 países, empregando cerca de 130 mil funcionários que geraram um faturamento global de 99 milhões de euros em 2017. Foram 2,5 milhões de carros das 3 marcas e 164 mil motocicletas, sempre buscando atingir um segmento premium.
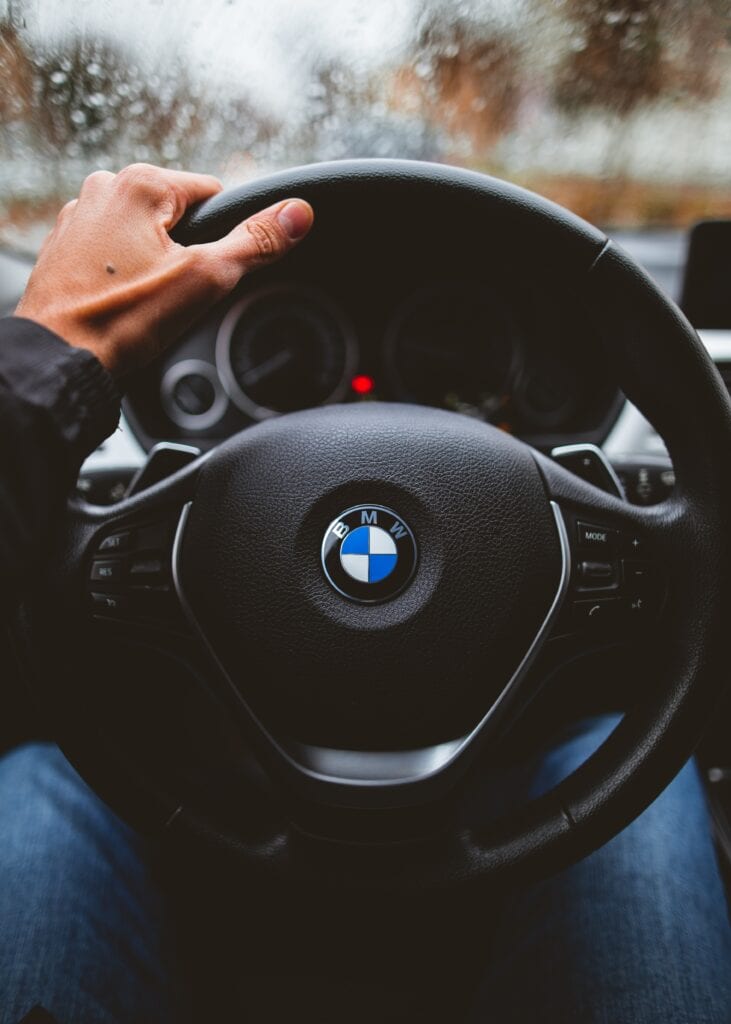
A fábrica de Altdorf centraliza a produção de componentes plásticos e metálicos, além de fabricação e reforma de motores. Lá pudemos conhecer os processos de produção de peças em plástico e resina, reforma de motores e fundição. É evidente a intensidade da tecnologia empregada na forma de robôs e grandes máquinas. Há dezenas de pequenos veículos automatizados trafegando pela planta dos motores, por exemplo. Mas até aí, ainda estamos na fase da indústria 3.0, que propagou a robótica. A diferença para agora é que todos os setores e unidades de negócios são interligados, a rastreabilidade do emaranhado de peças que compõe um veículo é total e toda a produção é integrada.
A digitalização da produção permitiu o fornecimento de materiais às plantas de forma rápida e flexível a condições variáveis.
Em uma escala menor do que na Siemens, o que é natural pelo tipo de produção, mas ainda de forma muito eficiente, a linha de produção pode ser ajustada em minutos, com equipamentos de algumas toneladas sendo manejados com facilidade pela sua modularidade.
Os serviços de reforma de motores, por exemplo, demandam uma infinidade de especificações e uma customização contundente da linha de trabalho, já que todos os motores da marca no mundo que apresentam qualquer necessidade de reparo estruturante são enviados para essa fábrica. São mais de 30 anos de evolução de motores, hoje entendidos num conceito de nuvem e automação.
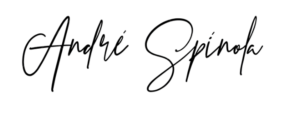